About Us
Revacco Refrigeration is an export leading supplier of commercial and industrial refrigeration equipment in Turkey. Our products and solutions have been used in recent years across the globe by caterers, restaurants and hotels, research centres, hospitals, pharmaceutical and food industries. We are dedicated to designing and manufacturing the highest quality products for the refrigeration markets around the globe.
Our clients and customers are supported through our manufacturing facilities in Ankara, and Konya. All our products are engineered and manufactured in accordance with European Union and International quality standards. We supply to the global market through a sales network operating in different cities. Our main sales representative offices are located in Antalya, Doha, Lagos, New York and Lima.
Over the years, our cold and freezer rooms, refrigeration systems ( condensing and evaporator units ), and thermal insulated doors have indeed proven it's durability. The aim of our product development is to bring into practice qualities appreciated by professionals – usability, cost-effectiveness, product safety and life-cycle management.
Engineering expertise and excellence belong to our DNA. majority of our team is made up of experienced engineers. All of us at Revacco are encouraged by creativity, fast responses and proactive adaptation to the latest market trends and needs.
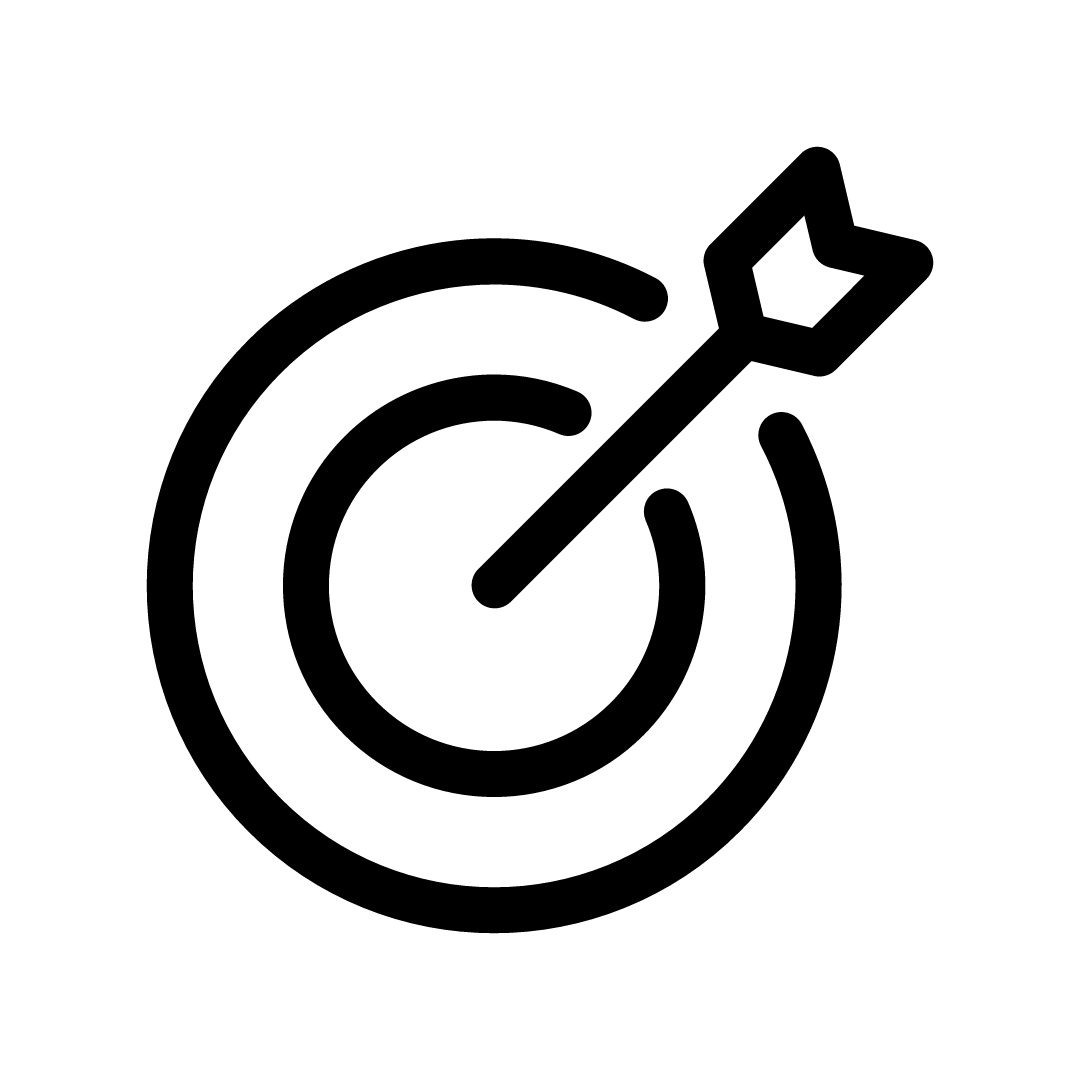
Mission
To develop and offer innovative solutions for a more reliable, efficient and sustainable operation of refrigeration facilities.
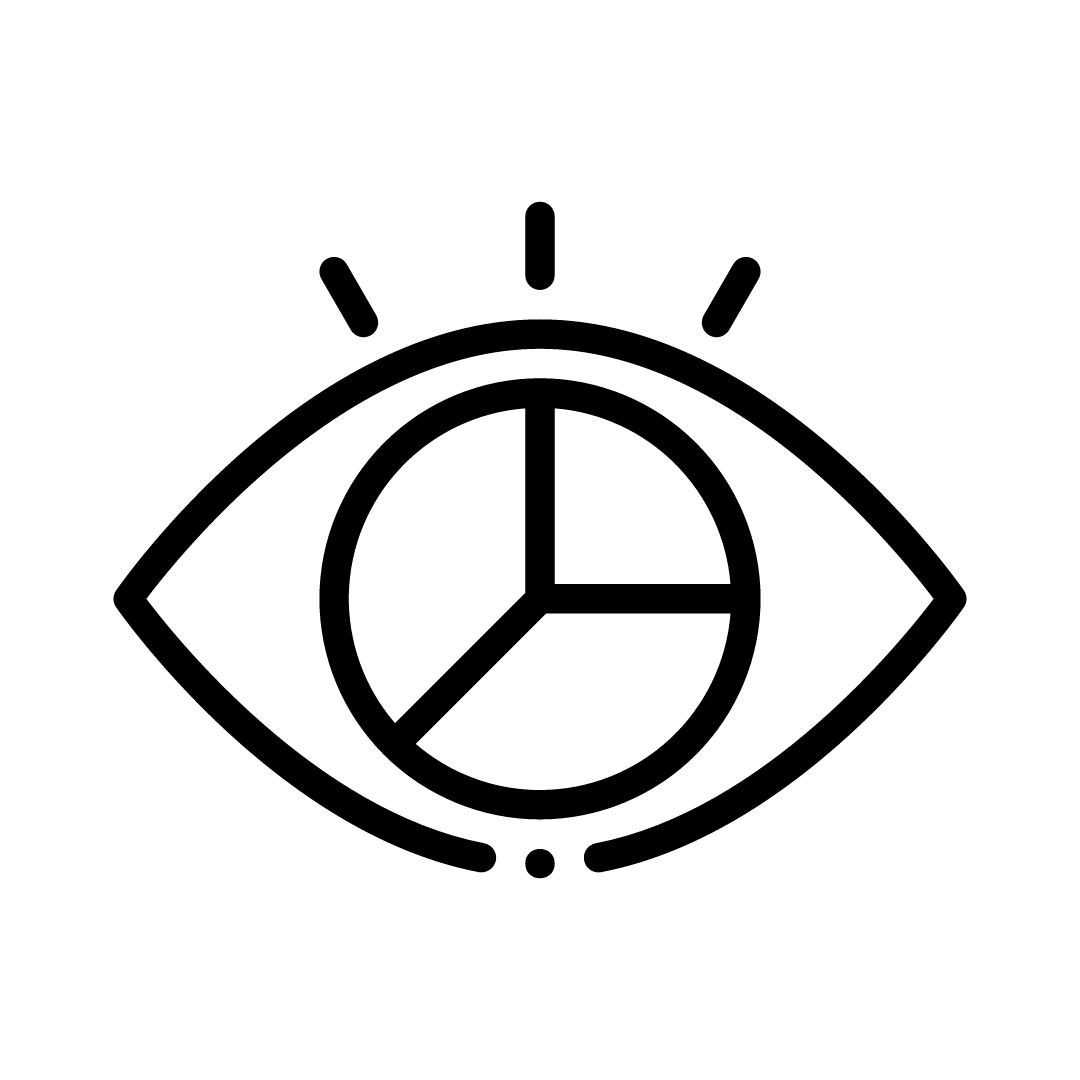
Vision
To build a brand reputation in the international markets as well as the first choice for our customers, and partners.
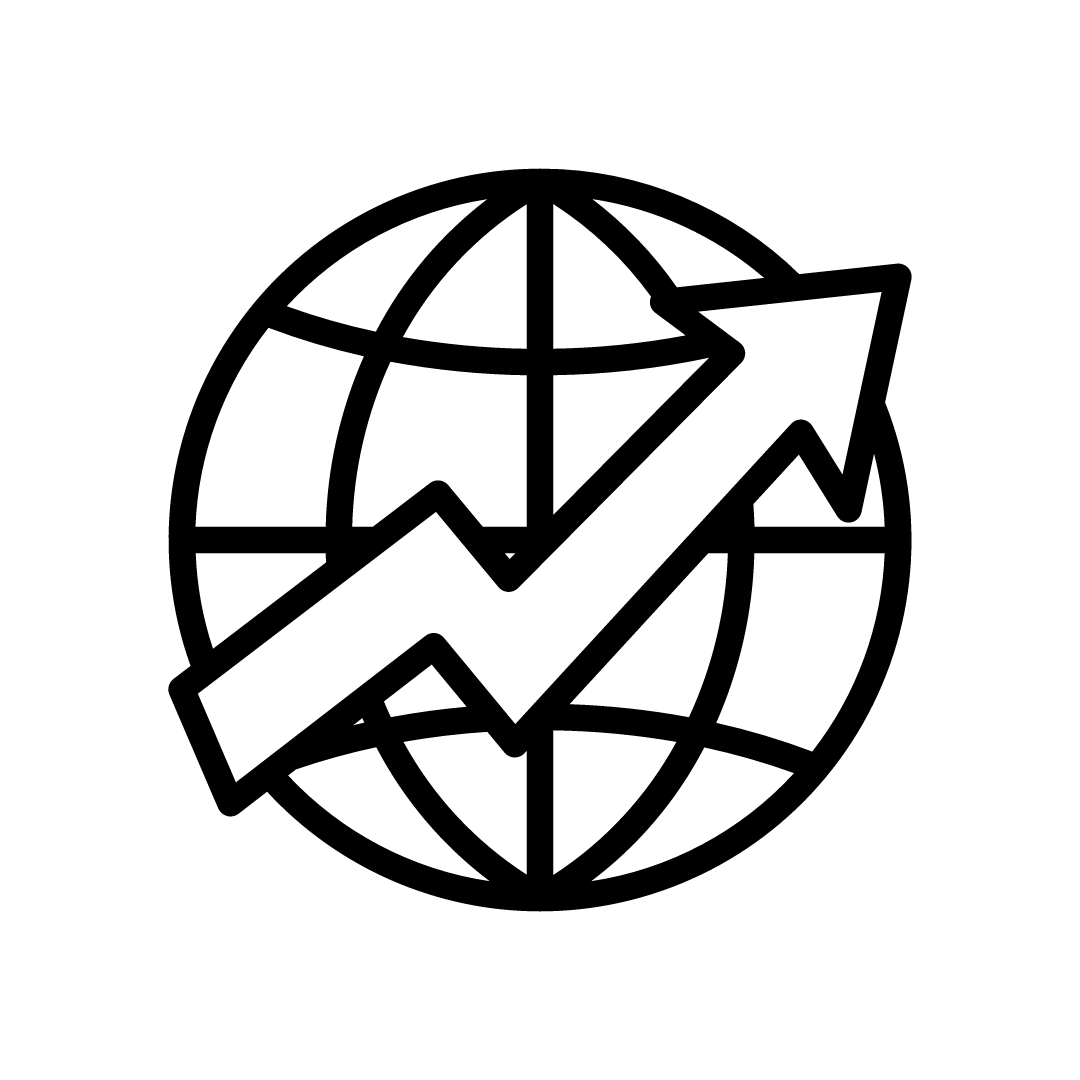
Strategy
To expand our business by broadening our product portfolio, our sales force and by promoting our customer's loyalty.
About Refrigeration
Industrial refrigeration is a specialized field that deals with cooling and freezing large-scale industrial processes and equipment. It is essential in food and beverage, pharmaceuticals, and chemical manufacturing industries, where temperature control is critical to maintaining product quality and safety
Industrial refrigeration systems are much larger and more complex than typical residential or commercial refrigeration systems, with components such as compressors, condensers, evaporators, and control systems designed to handle heavy-duty cooling loads.
The refrigerants used in industrial refrigeration systems often differ from those used in residential and commercial systems, as they must operate at much lower temperatures and handle higher pressures. Proper maintenance and servicing of industrial refrigeration systems are essential to ensure optimal performance and prevent costly downtime and product loss.
What is The Difference Between Commercial And Industrial Refrigerators?
Commercial refrigerators are typically smaller and used in restaurants, grocery stores, and convenience stores. These containers are intended for holding small amounts of food and beverages and are frequently utilized for presentation. Even though they are durable and can withstand continuous use, they are not suited for heavy-duty industrial use.
On the other hand, industrial refrigerators are much larger and designed for heavy-duty use in industries such as pharmaceuticals, chemical processing, and food production. They're typically used to store large quantities of temperature-sensitive products and are built to withstand harsh industrial environments. Industrial refrigerators often have more advanced temperature control systems and can maintain precise temperature ranges.
Key Components
An industrial refrigeration system has five core components: refrigerant, compressor, condenser, metering device, and evaporator. Below is a description of them:
Compressor
When refrigerant undergoes vaporization due to heat, it enters the compressor, a device that elevates the pressure and temperature of the vapor. For the refrigeration cycle to continue, the temperature must exceed the condensing fluid. The compressor functions as a pump to maintain refrigerant flow within the system.
An industrial compressor may belong to one of the following categories.
- Screw
- Piston
- Centrifugal
- Rotary
- Condenser
A condenser, or a coil, is where refrigerant goes after leaving the compressor. Generally, the condenser coil is exposed to something cool, which allows the refrigerant to release heat. The fluids can range from outdoor air to water to other types. As a result of heat release, the refrigerant condenses into a liquid. The main goal is to have the refrigerant at the same pressure when it leaves the condenser but cooler.
Industrial refrigeration uses three types of condensers:
Air-cooled – This method involves exposing the refrigerant to outdoor air to achieve cooling, utilizing a fan or blower to distribute the air across the entire area.
Water-cooled – A second tube containing refrigerant is usually employed with a water-filled tube. Water absorbs heat from the refrigerant.
Evaporative – This method is commonly used to transfer heat through water spray on the refrigerant coil, resulting in heated and moist air that a fan or blower expelled from the system. It's the most widely used of the three.
Metering Device
After leaving the compressor, the refrigerant enters the metering device. Here, it serves two important purposes. Firstly, it reduces the flow rate of refrigerant into the evaporator. Secondly, it decreases the pressure. Essentially, this device acts as a valve between the high and low-pressure components of the refrigeration system.
Evaporator
The final stage of the cycle involves the absorption of all unwanted heat. Like the condenser, this component is also a coil, but the refrigerant evaporates in this case. In industrial settings, the options for cooling are either air coil evaporators or liquid coolers.
Refrigerants
Refrigerants are liquids used to transfer heat between areas. These substances change form due to variations in temperature and pressure. For example, as the system's temperature increases, it transitions into a gaseous state. When it loses heat, it returns to its liquid form. As a result, the refrigeration cycle of heating and cooling is created.
Industrial refrigeration commonly uses ammonia and R-134a. R-134a is halogen-free and environmentally friendly. Ammonia is an older refrigerant but more efficient at absorbing heat. Other refrigerants available are carbon dioxide, hydrocarbons, and fluorocarbons.
The Use of Natural Refrigerants
As one of the key components, refrigerants have a significant role in the industrial refrigeration cycle. Many companies have switched to natural refrigerants in recent years.
The use of natural refrigerants in industrial refrigeration has become increasingly popular in recent years. Ammonia, carbon dioxide, and hydrocarbons are natural refrigerants with a lower environmental impact and are more energy-efficient than traditional synthetic refrigerants.
Types of Natural Refrigerants
There are three categories of natural refrigerants, as follows:
Carbon Dioxide (CO2) or R-744
This substance is frequently utilized in the automotive sector as a substitute for Hydrofluorocarbons (HFCs) due to its lack of impact on the ozone layer and low potential for global warming. It lacks both odor and color and is denser than air. Its Global Warming Potential (GWP) is equivalent to one.
Ammonia (NH-3) or R-717
Ammonia is the most commonly used refrigerant in industrial refrigeration and was previously used in home refrigerators. It's a naturally occurring compound that decomposes into hydrogen and nitrogen molecules, which make up 80% of the atmosphere. The ammonia refrigeration system operates using a closed cycle of evaporation, compression, condensation, and expansion.
Hydrocarbon-Based Refrigerants (HC)
These refrigerants are natural and don't harm the ozone. They have a low global warming potential of less than 5. These gases require expertise and precautions since they are flammable gases (A3 type). There are restrictions on using them as refrigerants with a load limit of 150 grams.
Benefits of Natural Refrigerants
Here are some benefits of using natural refrigerants in industrial refrigeration systems:
Environmentally friendly – Natural refrigerants have a lower GWP than traditional refrigerants such as hydrofluorocarbons (HFCs) and chlorofluorocarbons (CFCs). They don't contribute to ozone depletion or climate change, making them a more sustainable option.
Energy-efficient – Compared with conventional refrigerants, natural refrigerants require less energy to maintain the same level of cooling. This results in lower operating costs and reduced carbon emissions.
Cost-effective – Natural refrigerants' availability and lower GWP make them more cost-effective than conventional refrigerants. They also require less maintenance and have a longer lifespan, resulting in lower repair and replacement costs.
Safe – They're non-toxic, non-flammable, and non-corrosive, making them safer to handle and use than traditional refrigerants. They also have a lower risk of leakage, which reduces the risk of accidents and environmental damage.
Industrial Refrigeration Service and Maintenance
Neglecting maintenance can lead to costly breakdowns, lost productivity, and product spoilage. That's why having a reliable industrial refrigeration service provider is essential to keep your system in top condition.
Regular preventive maintenance can include checking refrigerant levels, inspecting electrical connections, cleaning coils, and replacing worn or damaged components. In addition, a service provider can perform preventative maintenance to identify potential problems before they become serious.